Navigating the world of warehouse management can feel like steering a ship through uncharted waters, especially when it comes to choosing the right material handling equipment for your warehouse. It’s not just about filling your space with the latest gadgets; it’s about finding the right tools that fit like a glove with your operations, boosting productivity, enhancing safety, and keeping costs in check. With so many options out there—each with its own bells and whistles—the journey to pinpoint your warehouse’s best match can seem daunting. But fear not! We’re here to guide you through this maze, offering clear, expert advice that will help you understand exactly what your warehouse needs. From weighing up the pros and cons of the latest tech to matching equipment capabilities with your specific demands, we’re here to ensure your choice not only meets but exceeds expectations.
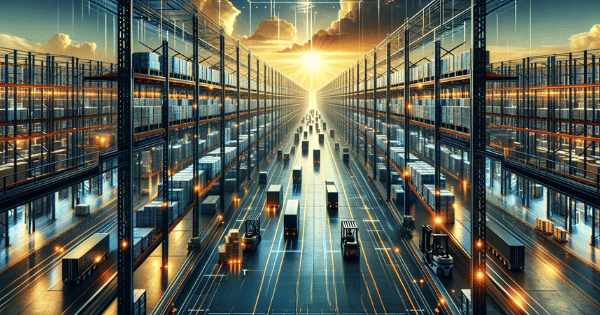
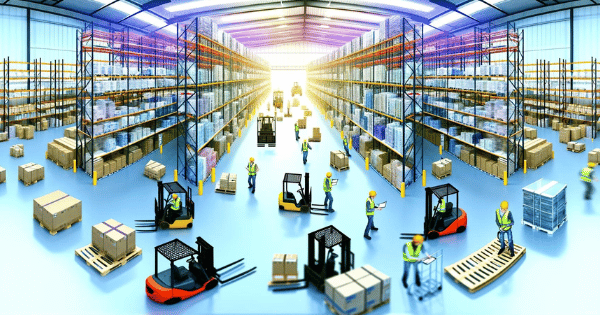
Understanding Your Warehouse Needs
The first step is to take a hard look at what your specific warehouse needs. This assessment is not just about the size of your warehouse or the volume of goods you handle; it’s about understanding the flow of operations, the nature of the goods stored, and challenges you face in your day-to-day operations. Here’s how you can start:
- Evaluate Your Space and Layout: The layout and physical dimensions of your warehouse significantly influence the type of equipment that will be most effective. Narrow aisles, high shelves, and special storage areas all call for different handling solutions.
- Analyze Goods Being Handled: The type, size, weight, and fragility of the goods you’re storing and moving play a crucial role in selecting the right equipment. Bulk materials require different handling systems compared to palletized goods or individual items.
- Consider Operational Volume: The volume of goods that move through your warehouse daily, seasonally, or annually will affect your choice. High-volume operations might benefit from automated solutions to keep up with the demand efficiently.
- Understand Your Workforce: The skill level and availability of your workforce can also dictate the kind of material handling equipment you should consider. Automated systems may reduce the need for manual labor but require a different skill set for operation and maintenance.
- Future-Proofing: Lastly, think about not just your current needs but also potential future growth. Choosing adaptable and scalable equipment can save significant time and resources as your business expands.
Taking a comprehensive look at your operations helps you identify the right material handling equipment to not only fit your current operations but also supports future growth. The right equipment choices can lead to smoother workflows, increased efficiency, and ultimately, a more profitable bottom line.
Types of Material Handling Equipment 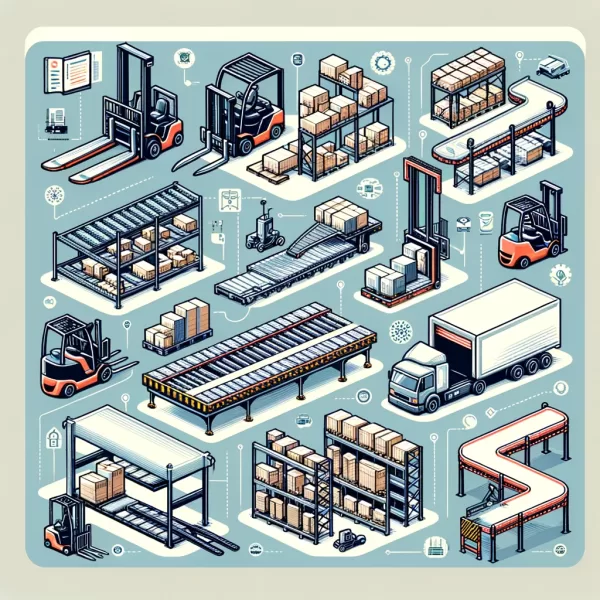
Navigating through the choices of material handling equipment can be overwhelming. But, understanding the types available and their specific uses can make the selection process much smoother. Here’s a rundown of some of the most common types of material handling equipment found in warehouses:
- Forklifts: The backbone of many warehouses, forklifts are versatile vehicles used for lifting, moving, and placing loads over short distances. They come in various types, including counterbalance, reach trucks, and pallet jacks, each designed for specific tasks and environments.
- Conveyors: Ideal for moving goods across different stages of the production or packing process, conveyors significantly increase efficiency. They vary from simple belt conveyors to complex roller systems and are particularly useful in operations with repetitive processes.
- Automated Storage and Retrieval Systems (ASRS): These automated systems are designed to store and retrieve goods with minimal human intervention. That makes them perfect for high-volume warehouses looking to maximize space and efficiency. They range from vertical lift modules to automated guided vehicles (AGVs).
- Pallet Racks and Shelving: Effective storage solutions are vital for maintaining order and maximizing space. Pallet racks and shelving units come in various sizes and configurations, tailored to accommodate different goods and warehouse layouts.
- Cranes and Hoists: For warehouses dealing with heavy or oversized items, cranes and hoists offer a practical solution. These devices can lift and move goods vertically and horizontally, making challenging materials easier to move.
- Sorting Systems: Automated sorting systems can expedite the process of organizing products for shipping or storage. They are particularly useful in distribution centers where speed and accuracy are paramount.
By matching the specific needs of your warehouse with the capabilities of equipment types, you end up with an efficient, streamlined operation that minimizes manual labor and maximizes productivity.
Factors to Consider When Choosing Equipment
Selecting the right material handling equipment isn’t just about what’s available; it’s about finding the perfect fit for your specific needs. Below are crucial factors to consider:
- Cost Efficiency: Budget constraints often dictate the choices made by warehouses. While it’s important to consider the initial purchase price , it’s also important to understand the long-term operating costs, including maintenance, repairs, and energy consumption.
- Space Utilization: The equipment you choose should maximize the use of available space. For instance, high-density storage solutions and equipment that can navigate narrow aisles effectively are critical for optimizing space, especially in smaller warehouses.
- Flexibility and Scalability: As your business grows, your material handling needs will change. For example, equipment with flexibility is a wise investment, allowing you to adapt without needing upgrades or replacements.
- Ergonomics and Safety: Worker safety and comfort are paramount. So, consider equipment that reduces the risk of injury and enhances productivity by being user-friendly and ergonomically designed.
- Technology Integration: In today’s digital age, choosing equipment that can integrate with your warehouse management system (WMS) or other technology platforms enhances efficiency, accuracy, and data collection.
- Environmental Impact: Consider the environmental footprint of your equipment. Not only do energy-efficient options help your company’s sustainability goals but they also reduce long-term energy costs.
- Vendor Reliability and Support: Lastly, the support and reliability of the vendor from whom you purchase your equipment are crucial. Look for vendors with robust support systems, warranty options, and a proven track record of quality.
Carefully weigh these factors to help you choose the right material handling equipment to serve you now and in the future.
The Impact of Technology on Material Handling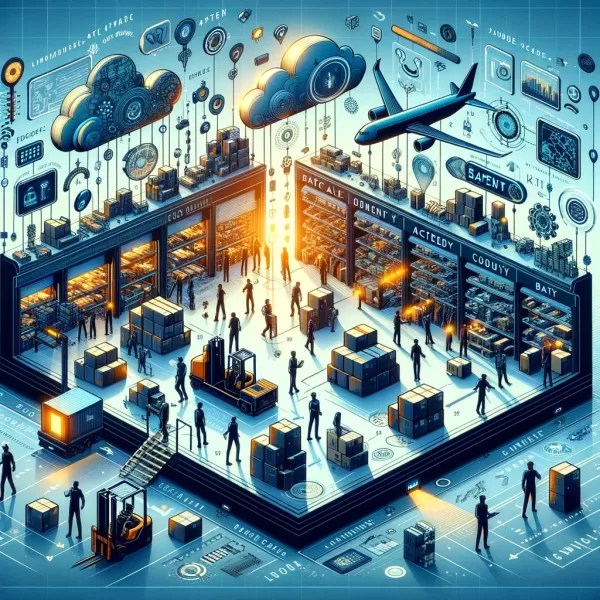
In recent years, the integration of advanced technology has revolutionized the landscape of material handling, ushering in a new era of efficiency, precision, and safety. From automation to robotics, these technological innovations are reshaping traditional material handling processes and redefining the capabilities of warehouses worldwide.
-
Automation:
Automation offers unparalleled levels of efficiency and productivity. Automated systems streamline workflows by reducing reliance on manual labor, minimizing errors, and accelerating throughput. For instance, automated storage and retrieval systems (ASRS) use robotic shuttles to retrieve and store goods with pinpoint accuracy, maximizing storage density and optimizing inventory management. Similarly, automated conveyor systems seamlessly transport goods throughout the warehouse, reducing bottlenecks and increasing throughput. By automating repetitive tasks, warehouses can achieve significant cost savings, improve order accuracy, and enhance overall operational efficiency.
-
Robotics:
Robotics increasingly provide warehouses with versatile and agile solutions to complex challenges. From robotic pickers that swiftly and accurately select items from shelves to robotic palletizers that efficiently stack and arrange goods, robots are revolutionizing warehouse operations. Not only do they enhance efficiency by performing tasks with precision and consistency, but they also reduce the risk of errors and minimize downtime. Moreover, robots can operate in hazardous or challenging environments, improving workplace safety and mitigating risks to human workers. By leveraging robotics, warehouses achieve higher levels of productivity, flexibility, and adaptability.
-
Data Analytics:
In addition to automation and robotics, data analytics plays a crucial role in optimizing material handling processes. By leveraging data from sensors, RFID tags, and warehouse management systems (WMS), warehouses gain valuable insights into their operations and make informed decisions to drive continuous improvement. Plus, data analytics enables warehouses to track inventory in real-time, predict demand patterns, and optimize inventory replenishment strategies. Moreover, advanced analytics algorithms can optimize warehouse layout and design, improve order picking routes, and reduce travel time. By harnessing the power of data analytics, warehouses can unlock hidden efficiencies and enhance decision-making capabilities.
-
Integration with Industry 4.0:
The integration of material handling equipment with Industry 4.0 technologies such as the Internet of Things (IoT), artificial intelligence (AI), and cloud computing is further driving innovation in the warehouse industry. IoT-enabled devices allow for real-time monitoring and control of equipment, enabling predictive maintenance and remote troubleshooting. AI-powered algorithms optimize warehouse operations by analyzing vast amounts of data and providing actionable insights for process optimization. Cloud-based software solutions facilitate seamless integration and collaboration across the supply chain, enabling warehouses to adapt quickly to changing market conditions and customer demands. By embracing Industry 4.0 technologies, warehouses can achieve higher levels of efficiency, agility, and resilience, positioning themselves for long-term success in the digital age.
The impact of technology on material handling is transforming warehouses into intelligent, interconnected, and highly efficient hubs of activity. By embracing these technologies, warehouses have unlocked new levels of productivity, efficiency, and agility, enabling them to thrive in today’s rapidly evolving business landscape.
Wrapping Up
Selecting the right material handling equipment is a critical decision that directly impacts warehouse efficiency and productivity. By understanding your warehouse’s specific needs, exploring various types of equipment available, and considering factors such as cost, space, adaptability, and technology integration, you can make informed choices that optimize your operations. Embrace the transformative power of technology and harness the capabilities of modern material handling equipment to propel your warehouse into the future of logistics excellence.
Visit our warehouse installation page to explore how we can elevate your warehouse game. Let’s be successful together!
As your Kansas City material handling and warehouse specialists, we’d love to discuss any projects with you! Call Single Source Systems at (816) 832-1622. Ask for Clint Aswegan, and he’ll answer all your questions.
Or click here to fill out our contact form or get a quote today!